Dry granulation is a granulation process in which raw powder is directly compressed into granules by mechanical extrusion. Usually refers to a granulation process that does not require the addition of liquids in the granulation process. So this is no need of drying and cooling. Namely, you can finish the fertilizer granule making at lower cost. For small-scale farms or fertilizer pellets manufacturers, dry granulation equipment are an inexpensive and convenient option.
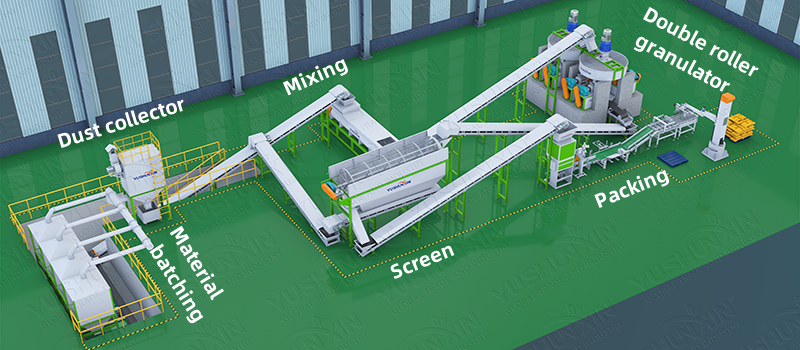
Dry Granulation Equipment
- Capacity: 1-3 t/h
- Types: double roller granulator, flat die granulation
- Final granules size: 1-10 mm
- Material: Carbon steel Q235/Alloy (stainless steel customized)
- Application: urea, ammonium chloride, ammonium phosphate, potassium chloride, bentonite, feed granules, organic fertilizer, etc.
Get more details about fertilizer dry granulation machine now !
What Machine is Used in Roller Compaction Dry Granulation?
In general, there are 2 types of dry fertilizer granulation machines for your choice. They can fully meet your requirements of both organic and compound fertilizer making in a small and large scales.
Double roller granulator for sale
If you want to make chemical fertilizer pellets, our double roller fertilizer granulator is you best choice. Including making NPK pellets, zeolite pellets, limestome granules,etc. The machine mainly makes use of roller extrusion to finish the dry granulation of chemical materials. There is no water involved, so you can reduce the cost of fertilizer granules drying and cooling. In addition, for large scale fertilizer granules production, you can setup a fertilizer granulation system with multiple roller granulators.
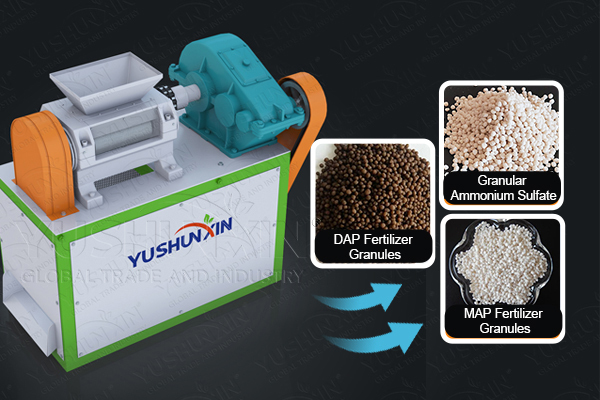
Double Roller Granulator
- Capacity: 1-3 t/h
- Power: 15-22kw
- Granule Shape: Flat ball
- Granule Diameter: 3-10mm
- Roller Sheet Size: 150*220mm
- Dimension: 1450* 80o*1450mm
- Color: green(can be customized)
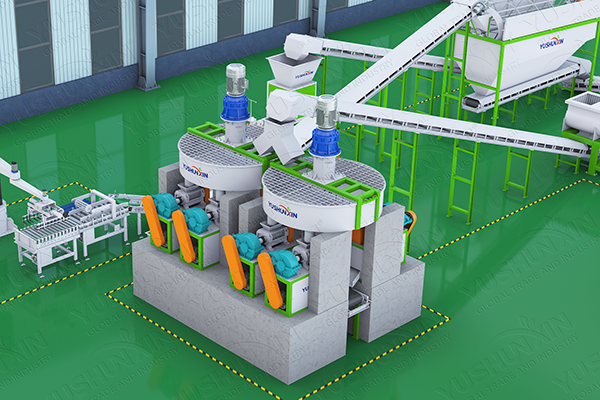
Flat die granulator for sale
But for manure to fertilizer or feed, we recommend you buy flat die pellet mill. It turn organic material into fertilizer pellets by roller pressing and blade cutting. After rotating roller press compost powder into the cylinder mold, you can get long fertilizer columns. Then cutting blade will divide them into short cylindrical pellets. Because dry granulation method employment, the feeding materials moisture must be lower than 10%. You can dry manure compost by natural sun or professional rotary dryer.
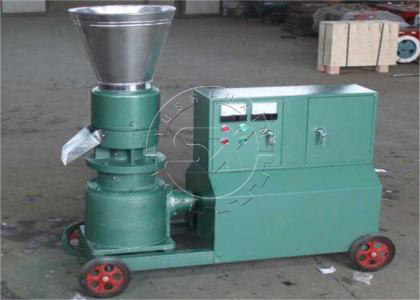
Flat Die Pellet Mill
- Capacity: 1-2.5 t/h
- Power: 30-45kw
- Granule Shape: Column
- Granule Diameter: 2-10mm
- Dimension: 630* 27o*750mm
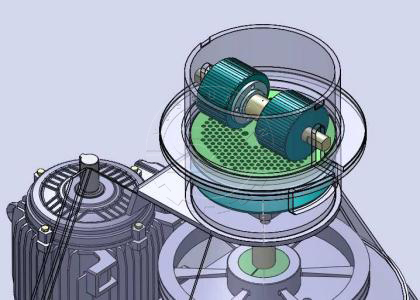
Why so many fertilizer manufactures make granules with dry granulation equipment?
Commonly, there are two kinds of method that used in fertilizer pellet manufacturing. But, from the feedback of our past customer – fertilizer manufactures all round the world, dry granulation equipment is popular in both the production of organic fertilizer granules and chemical pellets. So, why dry granulation machine is favoured than wet granulator? There are 3 reasons:
No drying and cooling – economical fertilizer granulation cost
As mentioned above, there is nearly no water involved in dry granulation of fertilizer. Therefore, compared with other fertilizer pelleting systems, it don’t need dryer and cooling to reduce the fertilizer moisture. In this way, you can prepare organic and compound fertilizer into granules at a lower investment.
Simpler process – less area for fertilizer pellet making
Because of no drying and cooling, fertilizer dry granulation line has a simpler process. By crushing, mixing, granulation, screening and packaging, you can sell produced fertilizer pellets to your customers. The less fertilizer equipment usually means less fertilizer plant area, which is is 1/3 smaller than other granulation production lines.
Roller pressing – higher hardness fertilizer granules making
Moreover, when granulating fertilizer powder with dry granulation equipment, you can get fertilizer pellets with a higher hardness. About 15-20N. Because roller pressing make material powder combine with each other more closely. With higher hardness, the finished fertilizer pellets are easier to transport, store and use.
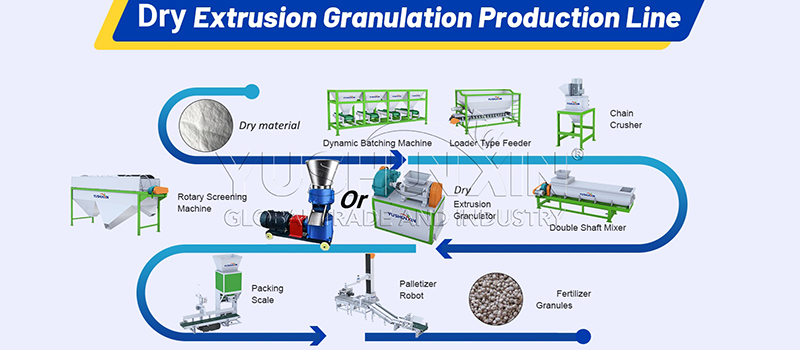
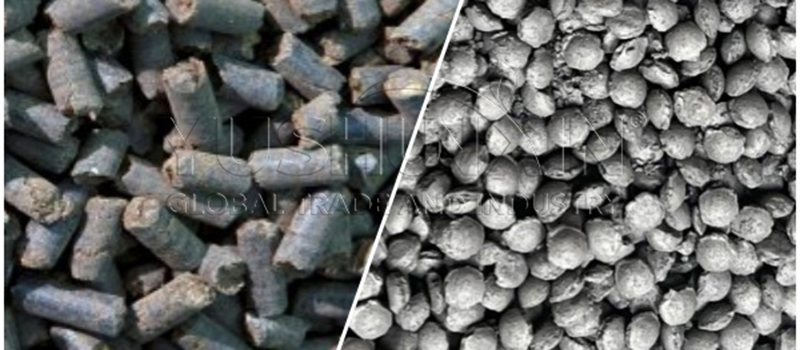
2 Conditions you need to focus on in dry fertilizer granulation
Usually, dry granulation equipment can make fertilizer pellets from various materials. Including, compost, bentonite, biochar, snow remover agent, NPK, graphite, lime, etc. However, the fertilizer materials for granule making need to meet the following 2 conditions:
Moisture lower than 10%
It is advisable to start dry granulation of fertilizer with low than 10% moisture materials. As the name suggests, the fertilizer granulation process is dry. Of course, including the dry granulation materials. So, you can reduce the possibility of material sticking to roller and produce fertilizer granules quickly. Therefore, it is the best choice for the granules making from raw material that are sensitive to moisture. Which will undergo chemical reactions when exposed to water or water vapor.
Material size between 0.1-1 mM
In addition, in order to make better fertilizer pellets, you also need to pay attention to the feeding material size in dry granulation. We recommend you keep it at 0.1~1 mm. When the raw material is finer than <0.1 mm, it will contain too much air. This will affects the extrusion process – increasing the vibration of the dry fertilizer extruder and the density of the final finished fertilizer granules. Adversely, large size feeding material requires more crushing energy.
When the dry granulation equipment is your best choice to make fertilizer pellets?
Then, it is necessary to use dry granule making machine when you granulate the following 2 kinds of powdery materials:
Ingredients that are sensitive to moisture
For one thing, when plan to use moisture sensitive raw materials to make pellets, dry granulation machine is your best choice. Or, the material will undergo chemical reactions and convert into another substance when exposed to water or water vapor. Such as urea, etc.
Material that are sensitive to temperature
For another, if you add temperature sensitive raw materials to fertilizer granulation process, we also recommend you buy a dry granulation mill. Because in the process of wet granulation, you need to dry fertilizer pellet. During drying, the finished fertilizer pellets will be damaged.
Get more details about fertilizer dry granulation machine now !
How to choose a reliable dry granulator machine manufacturer?
After deciding the model of dry granulation equipment you want to buy, it is necessary to find a reliable dry granulator machine manufacturer. So, you can purchase dry powder granulator with long service life, economical price, etc. In general, there are 3 tips for you.
Inquiring a leading and experienced granulator supplier
It’s essential to seek out a leading and experienced granulator supplier. Like YUSHUNXIN, an established provider with a history in the industry, is more likely to deliver high-quality dry extrusion equipment for fertilizer making. Their track record speaks to their expertise and reliability, ensuring that the dry granulation machine you purchase will meet your expectations in terms of performance and durability.
Looking for the source factory of dry granulation machine
Direct your search towards the source factory of the dry granulation machine. By dealing with the source factory, you sidestep intermediaries, which may reduce costs and provide more room for customization. Direct interaction with the factory allows for a clearer understanding of the manufacturing process, quality control measures, and technical capabilities, ensuring a higher standard of equipment.
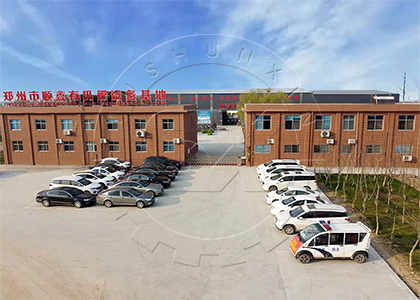
Finding manufacture with a considerate after-sale service
Lastly, don’t underestimate the importance of a manufacturer that offers considerate after-sale service. A dependable after-sales support system is crucial for the maintenance and longevity of your machine for dry granulation. Ensure the manufacturer provides comprehensive services, including installation, troubleshooting, maintenance, and the supply of spare parts. An attentive after-sales service not only enhances the machine’s lifespan but also assures ongoing efficiency and productivity in your operations.
Error: Contact form not found.