What are the Main Components of the New Type Organic Fertilizer Granulator?
The structure of the new organic fertilizer granulator consists mainly of the body part, the granulation rotor part and the transmission part. The driving device mainly includes a motor and a reducer, which provide power for the operation of the whole machine. The granulating rotor is the key to the whole machine. The design of the tooth granulator is compact in structure and stable in operation.
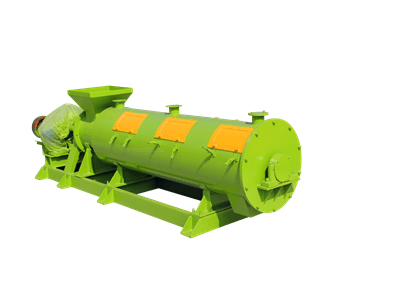
The Driving Device
The driving device of the tooth granulator lies in the left side of the whole machine. It consists of a motor and a reducer. The function of the motor is particularly important because the tooth granulator requires a huge amount of electrical energy to support it during operation. Our motor uses the internationally renowned three-phase asynchronous motors, which have the advantage of strong power and good running performance. The inside of the reducer is made of special materials and manufactured by a special process. High carrying capacity and stable operation.
The Granulating Part
The granulation part consists mainly of two parts: the barrel and the rotor.
The rotor
The rotor is the most important part of the stirring tooth granulator. The powder particles can be made into spherical particles by the high-speed operation of the rotor. It consists mainly of three parts: the shaft, the stirring tooth and the stirring tooth head. The large shaft is made of special material. The stirring teeth are also made of special materials, and you can adjust the length. You can disassemble and replace the stirring tooth head regularly.
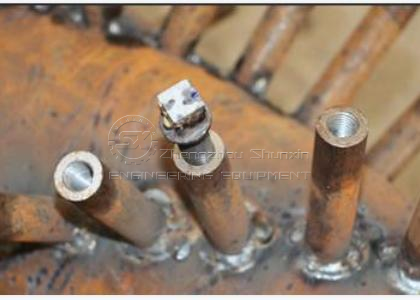
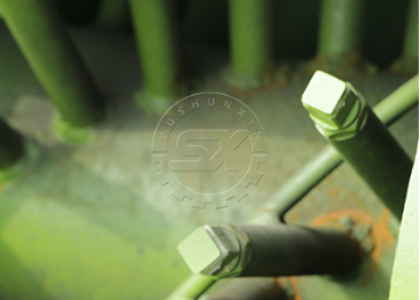
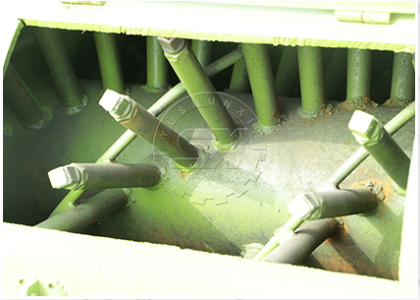
Barrel portion
The barrel is the shell we see wrapping the rotor. The barrel includes three parts: feed mixing section, granulation section and polishing section. The barrel is also made of special materials, which are hard and wear resistant.
The Body Part
The frame is the part that supports the operation of the whole machine. The stirring tooth granulator must be supported by a stable frame during operation.
How Does the New Type Organic Fertilizer Granulator Work?
The stirring tooth granulator is a kind of wet granulation. First, if your material is low in moisture, you should spray some water into the barrel while granulating. This will speed up the granulation process. When the material enters the machine from the feed port, under the action of mechanical force, it is made into granules by the rotation of the rotor. You can adjust the size of the particle diameter according to the rotational speed of the rotor. The higher the rotational speed, the smaller the particles. Before granulation, the moisture content of the raw material should be between 20% and 40%. The diameter of the finished particles is generally between 0.3-5mm.
How to Choose the Right New Type Organic Fertilizer Granulator?
We have different models of tooth granulators for you to choose from. Model SXJC-600, production capacity is 1-1.5 t/h, motor power is 37kw Model SXJC-800, production capacity is 1.5-2.5 t/h, motor power is 55kw Model SXJC-1000, production capacity is 2-4 t/h, motor power is 75kw Model SXJC-1200, production capacity is 4-6 t/h, motor power is 90kw Model SXJC-1500, production capacity is 6-8 t/h, motor power is 110kw
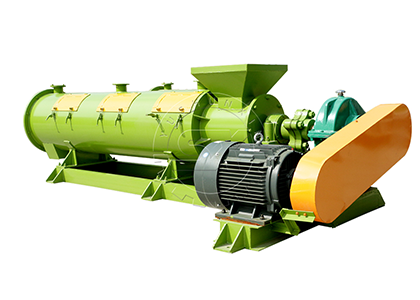
What is the Unique Design of Our New Organic Fertilizer Granulator?
High-strength Wear-resistant Material
In order to ensure the long-term operation of the stirring tooth granulator. We use some special material on some important parts. The material for the stirring teeth of our granulators is manganese steel. This steel is able to withstand huge impacts, extrusions, abrasions, etc. The teeth head of the granulator are made of carbide. You can disassemble and replace it. It is these special materials that have led many customers to choose SX.
Solid Triangular Base
In the design of the rack base, we use a triangular support design. Triangles are inherently stable. Strong support is essential for the smooth operation of the granulator in the presence of large rotational forces. And the use of square steel material makes the machine run more smoothly.
Observation Window
There is an observation window in the barrel of the granulator. On the one hand, the granulation situation can be observed in time. On the other hand, it is convenient for the inspection and maintenance of the machine.
Inlet and Outlet
The feeding port is designed on the top of the barrel. It is a square shape. Large diameter, convenient for feeding. The discharge port is designed on the lower side of the barrel. The entire barrel is installed with a certain inclination angle, and the discharge port is on the lower side. The prepared pellets can fall down to the discharge port along the barrel. Do not accumulate in the barrel.
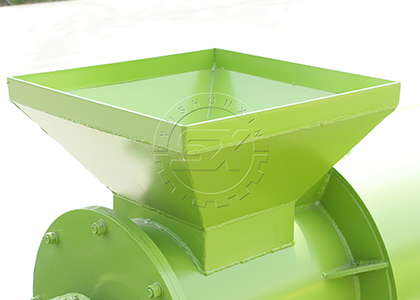
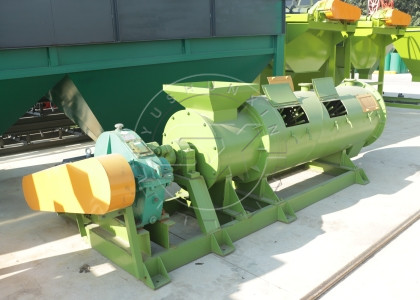
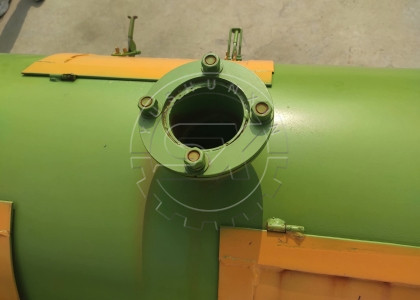
What are the Outstanding Advantages of the New Type Organic Fertilizer Granulator Compared with Other Granulators?
Fast Granulation Speed
Using the high speed rotating mechanical force and the resulting aerodynamic force, the powder materials are continuously mixed in the machine to realize granulation. The whole granulation process takes about 3-5 minutes from feeding to discharging. High granulation efficiency, more suitable for large-scale production. If you want to build an organic fertilizer production line, a tooth granulator is the right choice.
High Granulation Quality
This machine is especially suitable for the granulation of light and fine powder materials. The granules produced by the stirring tooth granulator have no edges and corners, and the one-time forming rate is high. And the particle hardness is better than that of disc granulator and drum granulator.
No Binder Required
Taking advantage of the fact that organic particles can inlaid and grow up with each other under a certain force, no binder is needed during granulation.
Wide Range of Material Sources
New type organic fertilizer granulator is mainly used for organic fertilizer granulation, such as cow, chicken, goat, pig and other livestock poultry manure. Agricultural crops, household waste, sludge, organic materials for food processing, alcohol residue, marsh residue, etc.
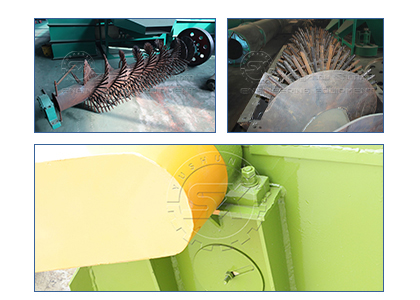
Things You Can Acquire When You Buy Our Granulator
(1) Before installation, the concrete foundation needs to be poured, and the equipment should be placed stably, otherwise it will affect the granulation. (2) Before starting the machine, check whether the joints of the machine are loose, and pay special attention to whether the stirring head is loose. (3) The reducer must be lubricated before use. After the first refueling operation for 100 hours, the new oil should be replaced. (4) It is strictly forbidden for iron blocks, stones, wooden sticks and other sundries to enter the machine to prevent damage to the machine. (5) When shutting down, the feeding should be stopped first, and the power should be turned off after the material in the machine is completely discharged. When it is not used for a long time, the materials in the machine must be cleaned to prevent sticking.
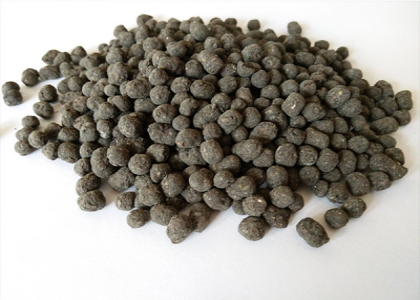
What Other Equipment do You Need When You Want to Build a New Type Organic Fertilizer Production Line?
Dynamic Batching Machine
When making compound fertilizer, you should mix a variety of raw materials. The dynamic batching machine is mainly fitting for mixing, batching and feeding of 3-8 kinds of materials. First of all, our dynamic batching machine can choose the number of bins. The most common is the four-bin batching machine. If you want to make compound fertilizer of several elements, you can choose several warehouses. Secondly, you can customize the size of our silo. Again, in terms of material, the contact part between the silo and the material is made of stainless steel. Finally, the dynamic batching machine is automatically controlled by a computer. And a pneumatic door is used to control the quantitative feeding of the main silo. After the material is mixed in the mixing bin, it is automatically sent out by the belt conveyor.
Double Shafts Horizontal Mixer
Why do you need to add a blender? This is because the material coming out of the batching machine is unevenly distributed. If you granulate directly, the distribution of nutrients in fertilizer granules is uneven. Some elements are abundant, and some are even missing. So the mixer is an indispensable step. Our double shafts horizontal mixer uses a double-shaft design to make the material more evenly mixed. Generally, after the dynamic batching machine, it is transported to the mixing tank by the belt conveyor. Homogeneous agitation is carried out by means of helical blades mounted on double shafts. It is worth mentioning that the spiral blades on the double shafts rotate in opposite directions, so that the material is mixed more evenly. The stirring blade is made of high-strength wear-resistant material, which has a longer service life.
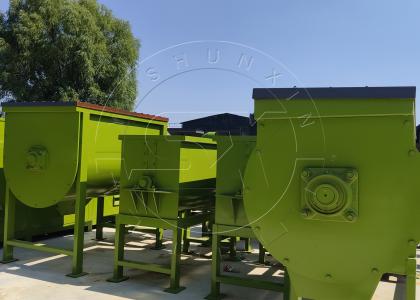
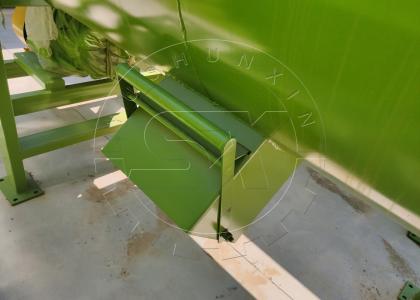
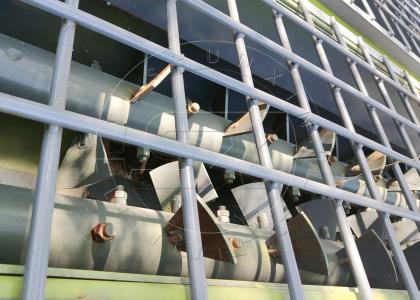
Rotary Screening Machine
The granules made by the roller extrusion granulator have different shapes and sizes. The function of the screening machine is to sieve out the powder particles and the particles whose shape is not up to standard. The screen of our screening machine is made of stainless steel, which prevents the material from corroding the screen. And with hitting anti-stick net device. The overall structure of the screening machine is made of 150 seamless tubes as the legs, 3mm iron plate as the box, channel steel as the frame, and 130 thick-walled seamless tubes as the shaft. In terms of material, it is tough and wear-resistant, and has a long service life. The powder screening machine has two discharge ports, one for finished products and one for waste products. The waste products are re-entered by the belt conveyor into the extrusion granulator for granulation. The finished product goes directly to the packaging process.
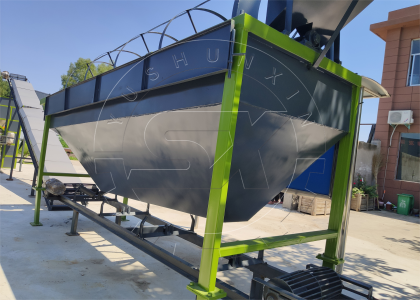
Belt Conveyor
Belt conveyor is an indispensable equipment for granulation production line. Mainly play the role of transport and connect each link. The belt of our conveyor is 4 layers canvas rubber belt with thickness 10mm. The frame part adopts 10mm international channel steel.
Packing Machine
The sieved particles can enter the final packaging process. Our packaging machines have an integrated design and are compact. Automatic packaging, quantitative weighing. The special design is that it can be fed and has bucket metering. The packing speed is fast and the packing precision is high.Using imported sensors, the measurement accuracy is plus or minus two thousandths.
Error: Contact form not found.