How Does Pan Granulator Work to Produce Fertilizer Pellets?
The disc granulator is considered to be the most widely used type of granulator. It is suitable for all kinds of powder granulation. Not only the granulation of organic fertilizer granulation, but also the granulation of other industries can use the disc granulator. What makes the disc granulator so successful is its high flexibility and special design. Our company’s disc granulator has been one of the best-selling granulators for several years. What is a disc granulator? Why do most customers choose it?
The disc granulator is a type of wet granulation. First, you should add water or steam to bond the powered dry material. Second, through the high speed rotation of the granulator, the granules in the pan squeeze and roll each other. Finally, they become spherical granules. In addition, the pan granulator is driven by motor and reducer drive. With the continuous rotation of the motor, the material continues to enter, it can achieve mass production. During the operation of the machine, the material rises with the pan, and the material is also moves down due to its own gravity. At the same time, the material is constantly thrown to the edge of the pan by the centrifugal force. The materials are from large granules to small granules under the action of these forces.
Pan Granulator
Model: SXYZ-6oo
Edge Height: 28omm
Rotary Speed: 33.5(r/min)
Capacity: 0.05-0.1 t/h
Total Power: o.75kw
Dimension: 800*7o0*950mm
What is the Uniqueness of the Design of the Disk Granulator?
Granular Plate
The granular plate is the big pan we see. Through the turning of the pan, the raw material turns into a ball on the plate. The minimum diameter of the granular plate is 500 mm, and the height of the plate is 200 mm. The maximum diameter can reach 3600 mm. The speed of the granulator with different diameters is also different. You can adjust the inclination of the granular plate, which determines the size of the granules. The overall adopts arc structure, the granularity rate can reach more than 93%.
Frame Part
The framework is the part that supports the entire machine. When the granulator operates, the force is relatively large. The framework must be made of a specific process to support the operation of the machine.
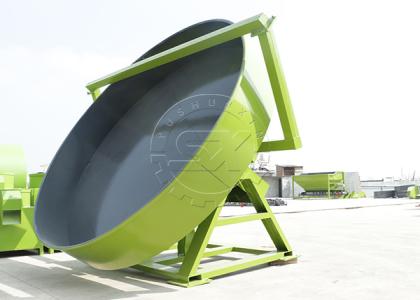
Adjustment Part
Adjust the size of the granules by adjusting the tilt angle of the granular plate.
The Transmission Part
The reducer and the motor use the flexible belt transmission to start smoothly and reduce the impact. Not only is it high efficiency, but it also improves the service life of the equipment. While the design of the transmission system improves the stability of the equipment, it also improves the service life of the components.
Cleaning Device
There is a scraper in the granular plate. While rotating the granular disc, the scraper rotates with the granular plate. Effectively prevents material from sticking to the pan.
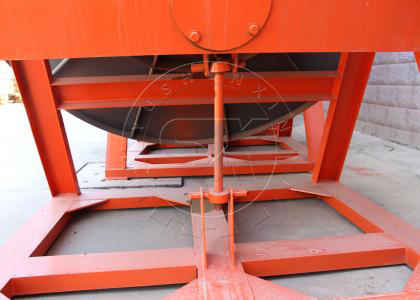
Where is the Core Advantage of our Equipment?
Different Models
For different production capacity, we have different models of pan granulators. If your raw materials are very small, we can give you a small granulator. There are small granulators with 0.5T/h output, and a large disc granulator with a 5T/h output. Of course, it is also appropriate to put the disc granulators on the production line.
Stable Base
When the disc granulator is running, the force is very strong. So it needs a stable and strong base to support. First of all, the two sides of the base of our granulators use the triangular structure design to make the equipment run more stable. Secondly, our framework is made of square steel, which has a strong supporting effect in shape and material. This also increases the stability of equipment operation.
Anti- Stick Wall Device
There is a scraper on the disc. When the discs are turning, the scraper will remove the materials that may stick to the plate wall. What are the benefits of it? On the one hand, it can keep your granules clean and you do not need to clean the granulator every day. On the other hand, it can reduce the consumption of raw materials and prevent the waste of materials.
Low Energy Consumption
When using a granulator, motor energy consumption is also one of the issues you consider. Our generators use internationally renowned three-phase asynchronous motors. The energy consumption of our generators and reducers can help you save more electricity. In addition, a flexible belt transmission between the generator and the reducer is transmitted to reduce the impact and extend the service life of equipment.
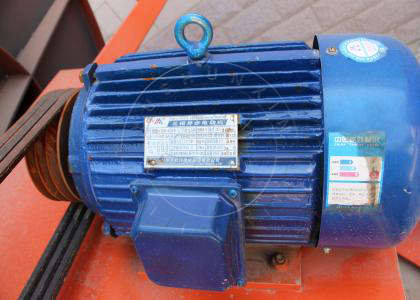
Water Spray Device
Given the stickiness of the raw material, we equipped the scraper with a water spray device. There is no need to manually add water, and the automatic water spray system saves manpower.
How to Choose an Ideal Disc Granulator for Your Production?
Small Disc Granulator
If you own a small fertilizer production plant, small disc granulators with diameters of 500mm and 600mm are suitable. Its production capacity is about 0.02-0.1t/h, which can meet your daily production of organic fertilizer granules.
Large Disc Granulator
Choosing the right type of granulator is critical for large fertilizer production plants. To a large extent, whether the production target can be achieved mainly depends on the type of granulator. We have large granulators with a production capacity of 4-6t/h. It has a diameter of 3600mm and a plate height of 450mm. This large disc granulator is also suitable for use in granulation lines. In the production line, the disc granulator can work continuously, relying on the belt conveyor to continuously feed the material and the disc to rotate continuously, so as to realize continuous production.
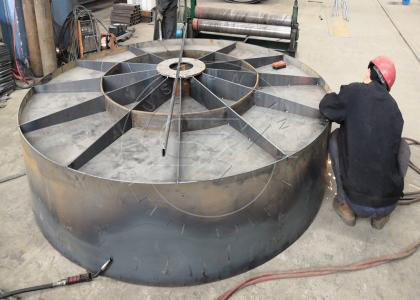
Organic Fertilizer Disc Granulator
The disc granulator is widely used for non-sticky materials in powder, material or small pieces. Livestock manure, such as sheep manure, chicken manure, cow manure, pig manure, etc, is fermented and turned like soil. So it is suitable for the granulation of organic fertilizer by the disc granulator.
NPK Disc Granulator
Similarly, the disc granulator is also suitable for the granulation of compound fertilizers. In the npk production line, many customers choose the disc granulator. Not only because of its high degree of granulation, but also because of its lower energy consumption and lower cost. The size and dimensions of our granulator can also be customized according to your needs.
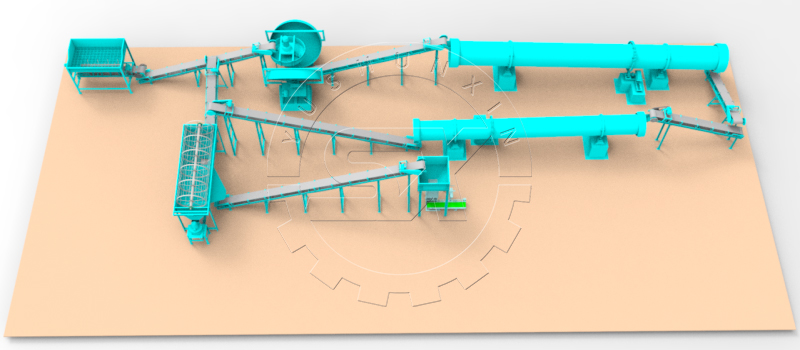
Tips on Using the Disc Granulator
Feeding Amount
You should maintain the appropriate amount during the operation of the disc granulator. Too much or too little will affect the granule size. Generally speaking, there will be a conveyor belt for uniform feeding on the production line.
Feeding Position
You should follow the rotation angle of the pan to feed. In this way, the material is subjected to greater force and the granule size is finer.
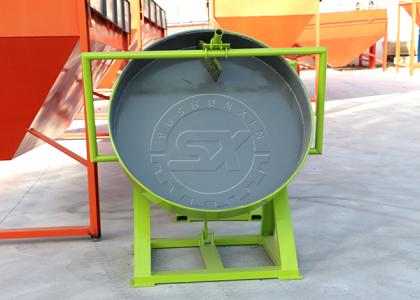
The Number of Sprays
When the material enters the disc granulator, it is necessary to add water to increase the viscosity between the materials for better roll formation. Our disc granulator has a water spray device above the scraper device. You can control the number of the water spray to adjust the material moisture. Less moisture, smaller granules. More moisture, larger granules.
Inclination of the Disc
The size of the fertilizer granule also depends on the inclination of the pan. The inclination is large and the granules are small. Smaller inclination, larger granules. You adjust the bolt at the bottom of the disc to change the position and angle of the reducer to achieve the purpose of normal use.
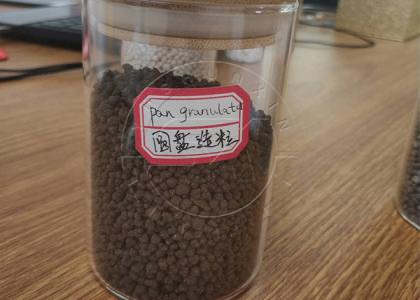
The pan granulator is simple in structure, easy to operate and easy to maintain. Since it is open, you can directly see the granulation situation in the pan, so it is easy to adjust. Under the action of centrifugal force, when the material in the disc reaches the required granules size, it will automatically come out from the edge of the disc. This results in a relatively uniform granule size of the product. Compared with the rotary drum granulator, the price of the disc granulator is lower and the required installation area is small. This is why the disc granulator is so popular.
Error: Contact form not found.